Extrusion History
Historical development of extrusion
Using an early model in 1797, Joseph Brama described a "press for producing seamless tubes of specified
diameter and length in lead and other soft metals" (Figure 1.4). Joseph Brama used molten lead, which
was pressed from one side to the melting chamber (A) with the help of a piston (B).
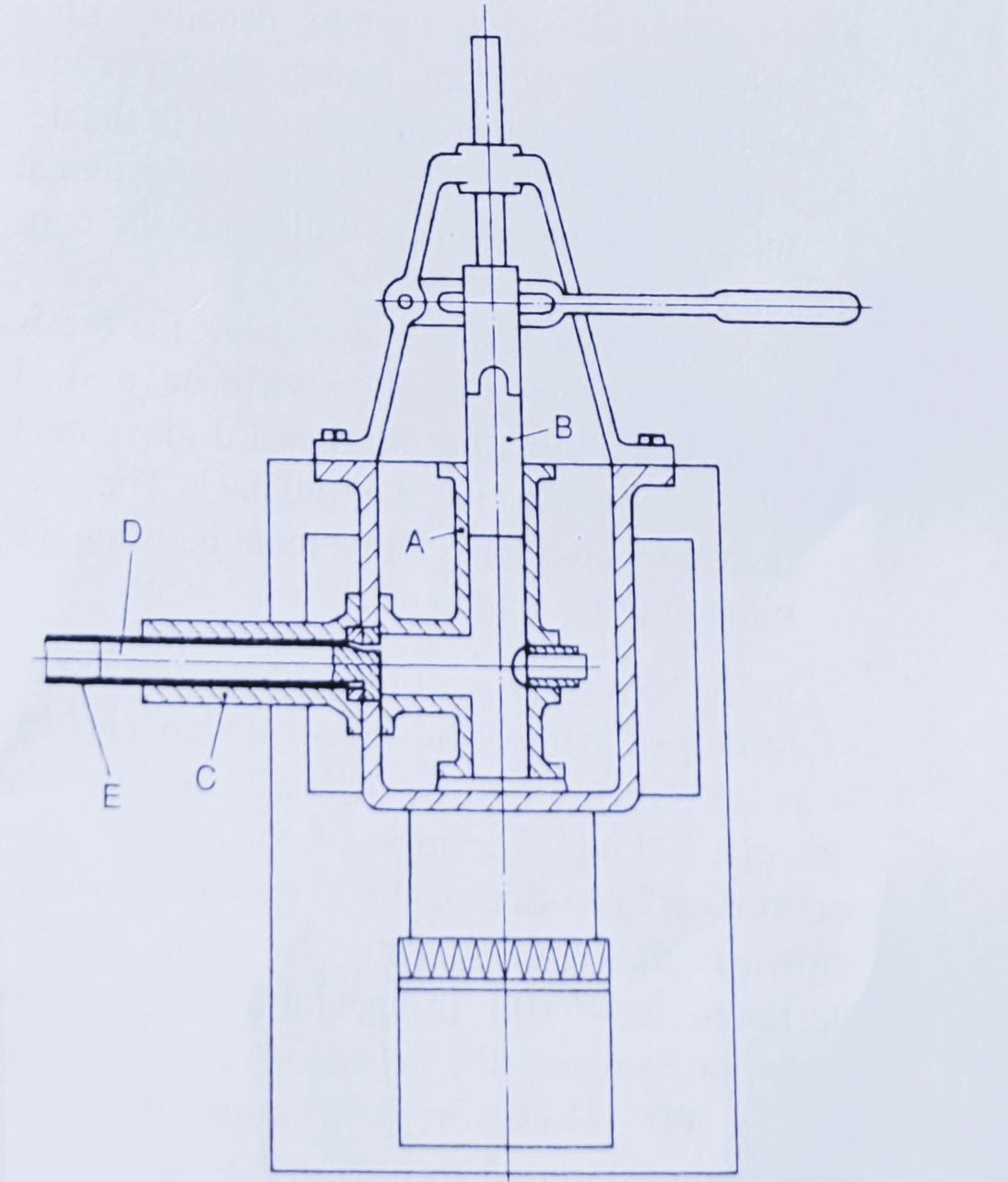
Figure 1.4: Brama lead pipe press, 1797. A, melting chamber; B, piston; C, tube support; D, tube
mandrel; E, extruded tube.
The molten material is then pushed by the piston as divided metal streams through the openings
in the mandrel so that the metal streams are combined and in the annular space formed by the
mandrel tube (D) and the tube support (C) to form a tube ( E) they become solid.
Pure lead melts at 327°C and most of its alloys at even lower temperatures, so this material can
be formed even at 80°C with low charges. Hence, lead was the only important extruded material
until the end of the 19th century. Many important elements of today's extrusion process were
developed during this period.
The first known design of a hydraulic (vertical) extrusion press for lead pipe was developed by an
Englishman named Thomas Burr in 1820 (Figure 1.5). This design consisted of a container (A),
an extrusion shaft with a machined pressure pad, a threaded mandrel, and a replaceable die (B).
Figure 1.5: The first vertical hydraulic press. A, container; B, template; C, extruded shaft and
machined mandrel; D, extruded tube.
England played a leading role in metal extrusion as well as in many engineering fields. Lead
pipes were used relatively quickly for water supply pipes.
English inventions from the 19th century include the bridge matrix, the hydraulic accumulator,
the gas-heated tank, and the indirect extrusion process.
Hanson, from 1837, produced lead pipes from a solid billet through a multi-part bridge matrix
with a replaceable pressure pad (Figure 1.6).
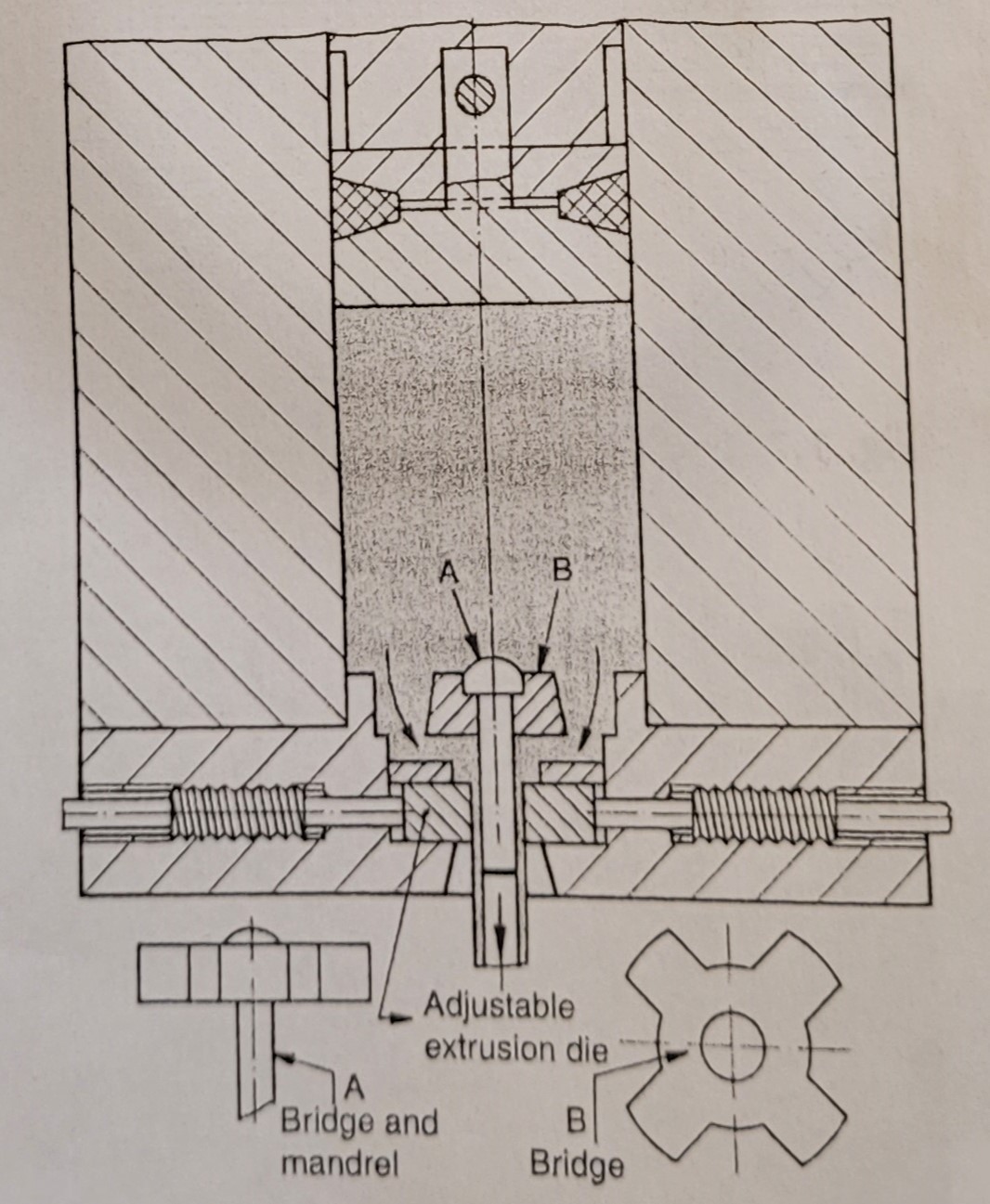
Figure 1.6 The first bridged mold The first gas-heated two-piece container was developed by Hamon
in 1867.
With the beginning of the use of electricity in industry, a new market was created for lead as a
coating material for power transmission cables.
The cable jacketing press was developed by Burrell in 1879 in which the lead was extruded directly
onto the cable core. This process was improved in 1882 by Werner von Siemens.
Alexander Dick, who lived in England, succeeded in developing the extrusion of metals with a
higher melting point using the experiences gained from lead extrusion. Hence, he is known as the
"Father of Extrusion".
In 1894, Alexander filed a patent for an extrusion press specifically designed for brass bars
(Figure 1.7). His idea was to pour liquid metal into a vertical tank and allow it to solidify.
After turning the tank horizontally, the product was extruded from this initial heat through a
replaceable matrix (F).
The direct water pressure pushed the piston forward. A pressure pad protected the water from
the heat of the billet and prevented extrusion in the photo direction. The mold and the mold holder
(E) were insulated against the cylinder head by two faces (D). These parts were opened at the end
of the process, and the mold and pressure pad were separated with the help of the extrusion shaft.
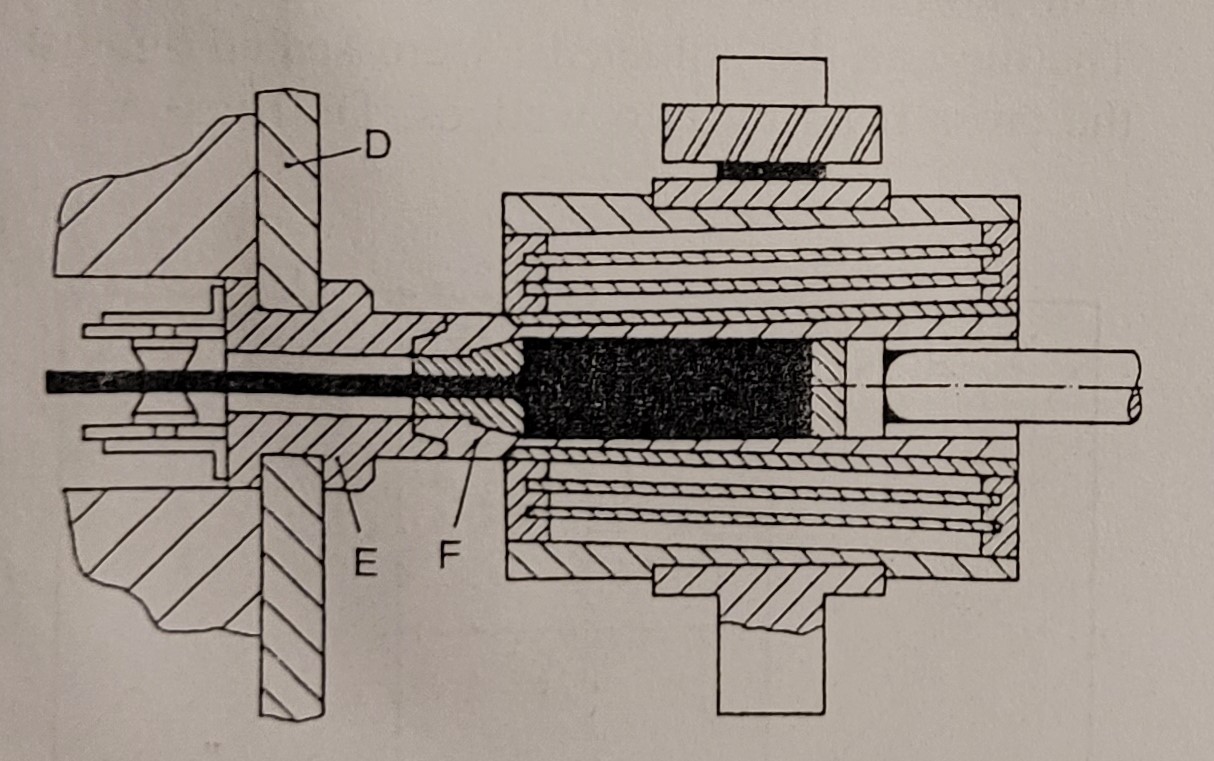
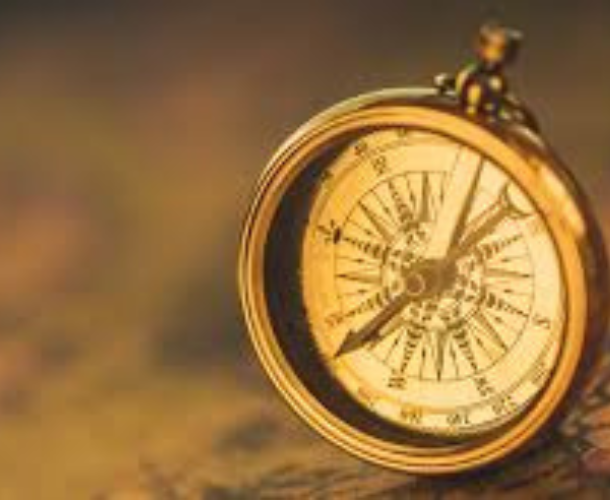