تاریخچه اکستروژن
توسعه تاریخی اکستروژن
جوزف براما به کمک یک مدل اولیه در سال 1797 یک "پرس برای تولید لولههایی با قطر و طول مشخص بدون درز در سرب و سایر فلزات نرم"
(شکل 1.4) را توصیف کرد. جوزف براما از سرب مذاب استفاده کرد که از یک طرف به اتاقک ذوب ( A ) به کمک پیستون ( B ) فشار وارد میکرد.
شکل 1.4: پرس لوله سرب براما، 1797. A، اتاقک ذوب؛ B، پیستون؛ C، پشتیبان لوله؛ D، ماندرل لوله؛ E، لوله اکسترود شده.
ماده مذاب سپس توسط پیستون به عنوان جریانهای فلزی تقسیم شده از طریق بازشوهای موجود در ماندرل فشار داده میشوند به طوری که
جریانهای فلزی ترکیب شده و در فاصله حلقوی تشکیل شده توسط ماندرل لوله ( D ) و پشتیبان لوله ( C ) برای تشکیل یک لوله ( E ) جامد میشوند.
سرب خالص در دمای 327 درجه سانتیگراد و بیشتر آلیاژهای آن حتی در دمای پایینتر ذوب میشوند، ، بنابراین این ماده میتواند حتی در دمای 80 درجه سانتیگراد با بارهای پایین شکل گیرد. از این رو، سرب تنها ماده مهم اکسترود شده تا پایان قرن نوزدهم بود. بسیاری از عناصر مهم فرآیند اکستروژن امروزی، در طی این دوره توسعه یافتهاند.
اولین طراحی شناخته شده از یک پرس اکستروژن هیدرولیکی (عمودی) برای لوله سربی توسط مرد انگلیسی به نام "توماس بر" در سال 1820 توسعه یافت (شکل 1.5). این طراحی دارای یک کانتینر( A )، یک شفت اکستروژن با یک پد فشار ماشینکاری شده، یک ماندرل رزوهای و یک ماتریس قابل تعویض ( B ) بود.
شکل 1.5: اولین پرس عمودی هیدرولیکی. A، کانتینر؛ B، قالب؛ C، شفت اکستروژن و مندرل ماشین کاری شده؛ D، لوله اکسترود شده.
انگلستان نقش پیشرویی در اکستروژن فلزات همچنین در بسیاری از زمینههای مهندسی داشت. لولههای سربی نسبتاً به سرعت برای لولههای آبرسانی مورد استفاده قرار گرفتند. اختراعات انگلیسی از قرن نوزدهم شامل ماتریس پل، انباشتگر هیدرولیکی، مخزن گرم شده به کمک گاز، و فرآیند اکستروژن غیرمستقیم میشوند.
"هانسون"، از سال 1837، لولههای سربی را از یک بیلت جامد از طریق یک ماتریس پل چند قسمتی با یک پد فشار قابل تعویض تولید میکرد (شکل 1.6).
شکل 1.6 اولین قالب دارای پل اولین کانتینر دو تکه که با گاز گرم میشد، در سال 1867، توسط "همون" توسعه یافت.
با آغاز استفاده از الکتریسیته در صنعت، بازار جدیدی برای سرب به عنوان ماده پوشش کابل انتقال برق ایجاد شد. اولین پرس پوشش کابل توسط بورل در سال 1879 ساخته شد که در آن سرب مستقیماً روی هسته کابل اکسترود میشد. این فرآیند در سال 1882 توسط ورنر فون زیمنس بهبود یافت.
الکساندر دیک، که در انگلستان زندگی میکرد، موفق شد با استفاده از تجربیات حاصل از اکستروژن سرب، اکستروژن فلزاتی با نقطه ذوب بالاتر را توسعه دهد. از این رو، او به عنوان "پدر اکستروژن" شناخته میشود.
در سال 1894، الکساندر طرح اختراعی برای یک پرس اکستروژن که به طور خاص برای میله برنج طراحی شده بود را به ثبت رساند ( شکل 1.7 ). ایده او این بود که فلز مایع را به داخل مخزن عمودی ریخته و اجازه دهد تا جامد شود. پس از چرخاندن مخزن به حالت افقی، محصول از این حرارت اولیه از طریق یک ماتریس قابل تعویض ( F )، اکسترود میشد. فشار آب مستقیم پیستون را به جلو هل میداد. یک پد فشار، آب را از حرارت بیلت محافظت کرده و از اکستروژن در جهت عکس جلوگیری میکرد. قالب و نگهدارنده قالب ( E ) در برابر سر سیلندر توسط دو وجه ( D )، عایق شده بودند. این قطعات در آخر فرآیند باز میشدند، همچنین جدایش قالب و پد فشار به کمک شفت اکستروژن انجام میشد.
شکل1.7 : اولین پرس اکستروژن برنج؛ D، گوه ها؛ E، قالب و نگهدارنده قالب؛ F، قالب قابل تعویض
چون کانتینر از جنس چدن یا فولاد بصورت یکتکه ساخته میشده، تمایل به ترک خوردن تحت تنشهای حرارتی بوجود آمده بدلیل ریختهگری فلز داغ داشت، از این رو، یک کانتینر چند تکه در سال ۱۸۹۶ معرفی شد. با این حال، سیلندرهای جداگانه قبل از فرآیند تحت فشار قرار نمیگرفتند بلکه تنها با گرافیت پودری و بوراکس از یکدیگر عایق شده بودند.
شکل 1.8؛ اولین پرس اکستروژن هیدرولیک
فرآیند وقتگیر کپی شده از اکستروژن لوله سربی که شامل پر کردن ظرف با فلز مذاب بود، به زودی با استفاده از بیلتهای ریختهگری پیشگرم جایگزین شد. الکساندر دیک طی یک دوره زمانی جزئیات مهم بسیاری را در اختراعات متعدد ارائه کرد که شامل: پد فشاری آزاد، طرحهای مختلف ماندرل برای لولهها، قالبها چند سوراخ برای اکستروژن و حتی یک قالب با مقطع توخالی ( Hollow ). قالب پل سه بخشی که توسط الکساندر دیک در سال ۱۸۹۷ اختراع شد در شکل ۱.۹ نشان داده شده است. بیلت به شش جریان تقسیم میشود که در دهانه شکلدهی به هم جوش میخورند.
شکل 1.9 قالب با نوآوری پل
تولید پرسهای اکستروژن با ظرفیتهای فشار بیش از ۷ مگانیوتن امکان استفاده از بیلتهای بزرگتر را فراهم کرد، که این امر، فرآیند اکستروژن را اقتصادی تر کرد. پرس اکستروژن هیدرولیکی آبی توسط یک سیستم آب فشار قوی که شامل پمپها و مخازن بود، به کار انداخته میشد. بیلتهای داغ به صورت دستی با استفاده از انبردست به داخل کانتینر بارگیری میشدند. شیرهای دستی برای کنترل توالی عملیات پرس اکستروژن استفاده میشدند. محصولات اکسترود شده باید به صورت دستی با انبردست کنترل میشدند.
توسعههای سریع در ابتدای قرن بیستم منجر به جایگزینی کامل فرآیند اکستروژن با فرآیند استاندارد قبلی برای تولید میلهها، مقاطع و سیم آلیاژهای مسی از مقاطع به کمک رولینگ بیلتهای ریختهگری شد. بیش از ۲۰۰ پرس اکستروژن، عمدتاً برای برنج، تا سال ۱۹۱۸ ساخته شده بود (عمدتاً توسط شرکت آلمانی کروپ-گروسون). با این حال، در آن زمان، مقاطع فولادی نیز تا سال ۱۹۱۴ به کمک اکستروژن تولید میشدند.
اگرچه امکان تولید لولهها در پرسهای استاندارد با توسعه "ماندرلهای شناور" که در بیلت توخالی آزاد بودند و رفته رفته به سمت قالب به شدت کوچک میشدند وجود داشت، اما این روش پس از اختراع "آرنولد شویگر" در سال ۱۹۰۳ با یک سیستم سوراخزنی جایگزین شد که در پشت سیلندر اصلی قرار داشت (شکل ۱.۱۰).
شکل ۱.10
نگهدارنده ماندرل که از سیلندر اصلی عبور میکند، ماندرل را در نوک خود حمل میکند و میتواند بیلت جامد را سوراخ کند. این فرآبند در ادامه شکل داخلی لوله را در قالب تشکیل میدهد. این پرسها که طبیعتاً میتوانستند برای اکستروژن میلههای توپر با حذف ماندرل نیز استفاده شوند، تا دهه ۱۹۵۰ ساخته میشدند. در ادامه با توسعه سوراخزن داخلی، امکان کوتاه کردن طول پرس و بهبود تراز ماندرل فراهم شد (شکل ۱.۱۱).
شکل 1.11: پرس اکستروژن لوله همراه با یک سوراخزن داخلی
در دهه 1920، تجربه نشان داد که هممرکزی دیوارههای داخلی و خارجی لوله در پرسهای هیدرولیک عمودی به دلیل تأثیر مثبت جاذبه بهتر است. ماندرل به محکمی به شفت پرس چسبیده و از بیلتهای پیشسوراخ شده استفاده میشد. در دهه 1950، تعداد زیادی پرس لوله عمودی (توسط شرکتهایی مانند شلومان و هیدرولیک) ساخته شد، اما این بار با حرکت مستقل ماندرل و عملیات خودکار برای تولید لولههای مسی و برنجی. تولید پرسهای عمودی حدود سال 1965 زمانی متوقف شد که امکان بهینه کردن مرکزیت پرس بهینه شد. هدایت بهتر کانتینر، شفت پرس و مندرل، کمک شایانی به تولید لولههایی با هممرکزی مناسب بود که در پرسهای افقی تولید میشدند. با وجود سرعتهای بالای چرخه تولید، پرسهایی با حداکثر ظرفیت ۱۶ مگانیوتن، قدرت کافی برای تحمل بیلتهایی با اندازه مناسب را نداشتند. حدود سالهای ۱۹۳۳، پرسهای مکانیکی عمودی لوله که توسط سینگر اختراع شده بودند، شروع به تولید انبوه لولههای فولادی کردند. این پرسهای عمودی با تعداد ضربات بالا در دقیقه برای تولید انبوه لولههای فولادی، عمدتاً جایگزین فرآیند نورد شده بودند که با بهرهوری بالاتر و صرفهجویی اقتصادی بیشتری کار میکردند.
کانتینر ها، که برای مدت زمان طولانی به صورت چند تکه اما بدون هرگونه اتصال دیگری تولید میشدند، تنها میتوانستند با فشار محدود پرس در حدود N/mm²300 کار کنند. با معرفی کانتینرهای پیشفشاری دو یا سه تکه بود که امکان استفاده از فشارهای اکستروژن بالاتر فراهم شد. کانتینرهای متحرک امکان بارگیری بیلت و حذف مواد زائد ( ته بیلت ) را فراهم کردند. معرفی گرمایش الکتریکی (گرمایش مقاومتی و بعداً گرمایش القایی) کانتینر در سال ۱۹۳۳، جایگزین گرمایش گازی یا زغالی شد و امکان اکسترود آلومینیوم را فراهم کرد (شکل 1.12).
شکل 1.12 : کانتینر سه تکه همراه با گرمایش القایی
از سال 1925، گسترش سریع فناوری اکستروژن منجر به تحقیقات گسترده در رابطه با پروسه جریان و نظریههای تغییر شکل شد. این تحقیقات منجر به توسعههای جدید در ساخت پرس و تولید ابزار شد. برای مدت زمان طولانی، رویه استاندارد طراحی هر پرس، مطابقت با نیازهای کاربر و مشتری بود. حدود سال 1960، پرسهای اکستروژن چند منظوره که به صورت همگانی قابل استفاده بودند در اروپا توسعه یافتند.
اگرچه شرکت آلکان از سال 1918 فرآیند اکستروژن آلومینیوم را با استفاده از پرسهای افقی انجام داد، پیشرفت چشمگیر در اکستروژن آلومینیوم با ساخت کشتیهای هوایی و هواپیماها آغاز شد. آلیاژهای آلومینیوم استحکام بالا با اکستروژن دشوار در دهه 1930 (آلومینیوم مس) توسعه یافتند، محصولاتی با مقاطع بزرگ از این حنس نیازمند پرسهای قدرتمند بودند. بزرگترین پرسهای اکستروژن ساخته شده تا سال 1945، دارای قدرت 125 مگانیوتن بودند. حدود سال 1950، پرسهایی با چرخه کوتاه و از پیشساخته شده با درایو روغنی مستقیم متغیر (نصب شده بالای پرس)، و جابه جا کننده قالب همراه با چرخش قالب برای تعویض سریع، در ایالات متحده توسعه یافت. این امر چرخههای بلاسود تولید را کوتاه کرد. این پرسها برای آلیاژهای آلومینیوم با بارهای 10 تا 30 مگانیوتن ساخته شدند. این پرسها در ترکیب با کوره بیلت گازی سرعت بالا در جلوی پرس و سیستم کنترل همراه با استرچر و اره، فرآیند تولید را بیش از پیش بهینه کردند.پس از آن، به کمک این فنآوریها، امکان تولید پنجره و ستون نمای آلومینیومی بصورت اقتصادی فراهم شد. چیدمان کامل یک کارخانه اکستروژن آلومینیوم در شکل 1.13 نشان داده شده است.
شکل 1.13 : سوله کامل اکستروژن آلومینیوم( SMS Hasenclever )
آزمایشهای R. Genders (1921، در انگلستان) برای اکستروژن غیرمستقیم، منجر به تولید این پرسها تا سال 1925 شد، پیشرفت و توسعهی این فرآیند تولید در گرو اکستروژن غیرمستقیم سیم برنج (شرکت هیدرولیک) بود. طراحیهای بهبود یافته و کاربرد آنها با استفاده از آلیاژهای آلومینیومی دشوار برای اکستروژن، کاربرد فزاینده فرآیند اکستروژن غیرمستقیم را تضمین کرد.
در مقابل، علیرغم تحقیقات گسترده و مقالههای متعدد، فرآیند اکستروژن هیدرواستاتیک تنها در کاربردهای بسیار تخصصی بعمل گرفته شد. یک نمونه از این تحقیقات، اکستروژن مواد مرکب ( کامپوزیتها ) است.
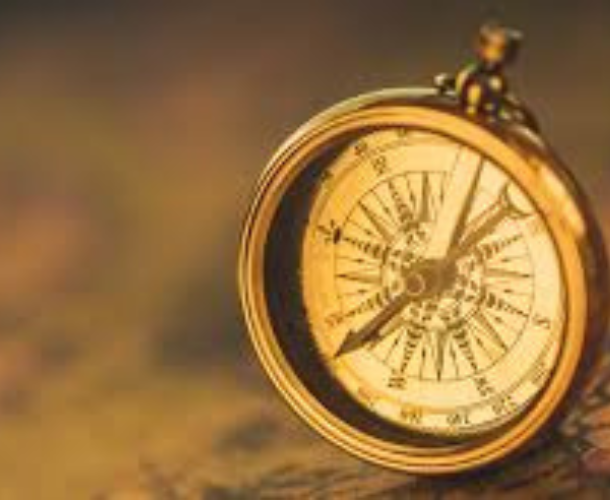